Remote Plasma Differentials
Remotely Generated Plasma enables new coatings on new materials
We have independent control of process parameters including target voltage and ion current which enables the deposition of high-quality thin films that can be difficult to produce using other deposition technologies such as magnetron.
Ion density (controlled by Plasma Source RF) and ion energy (controlled by target voltage) are independent.
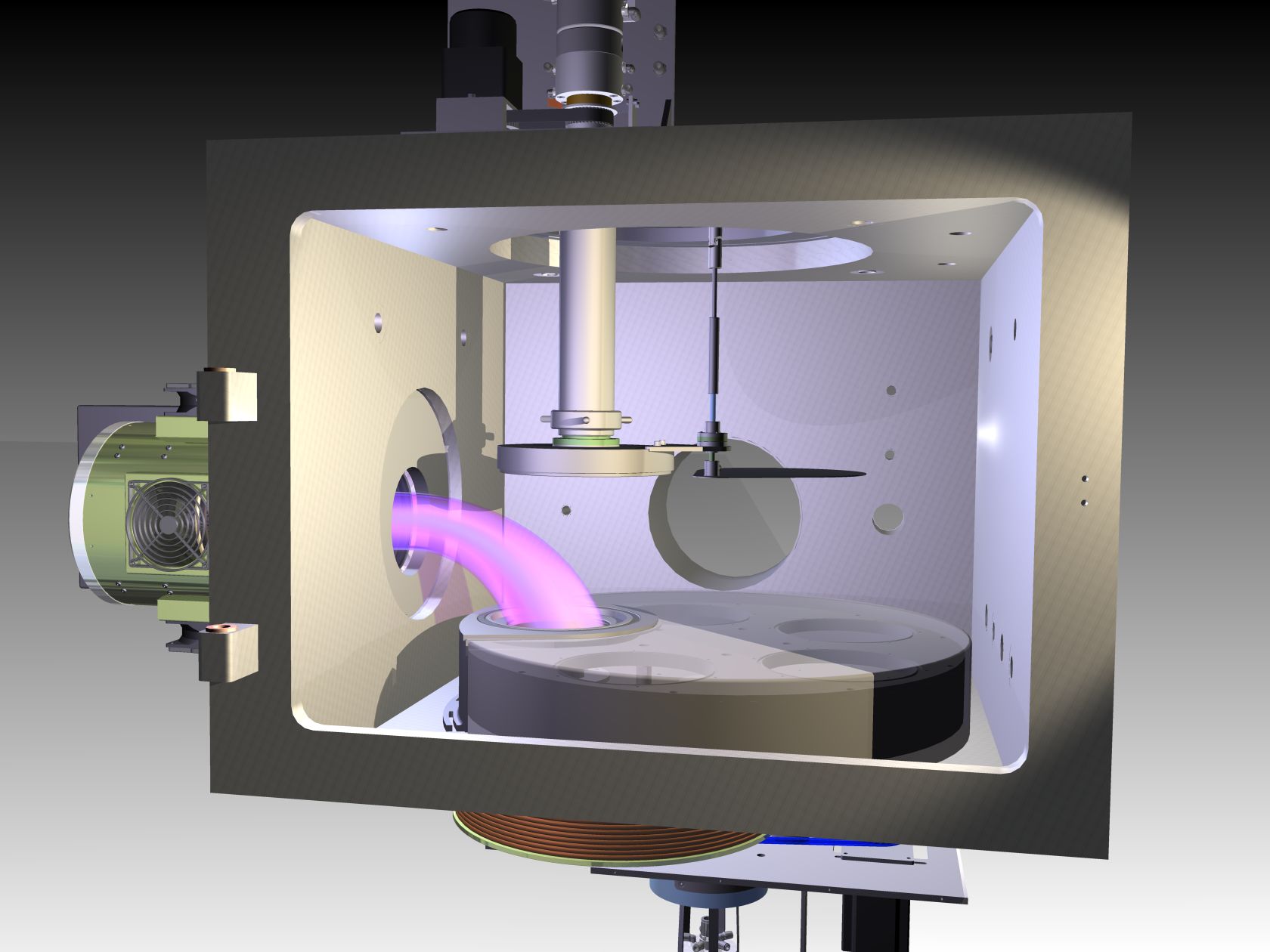
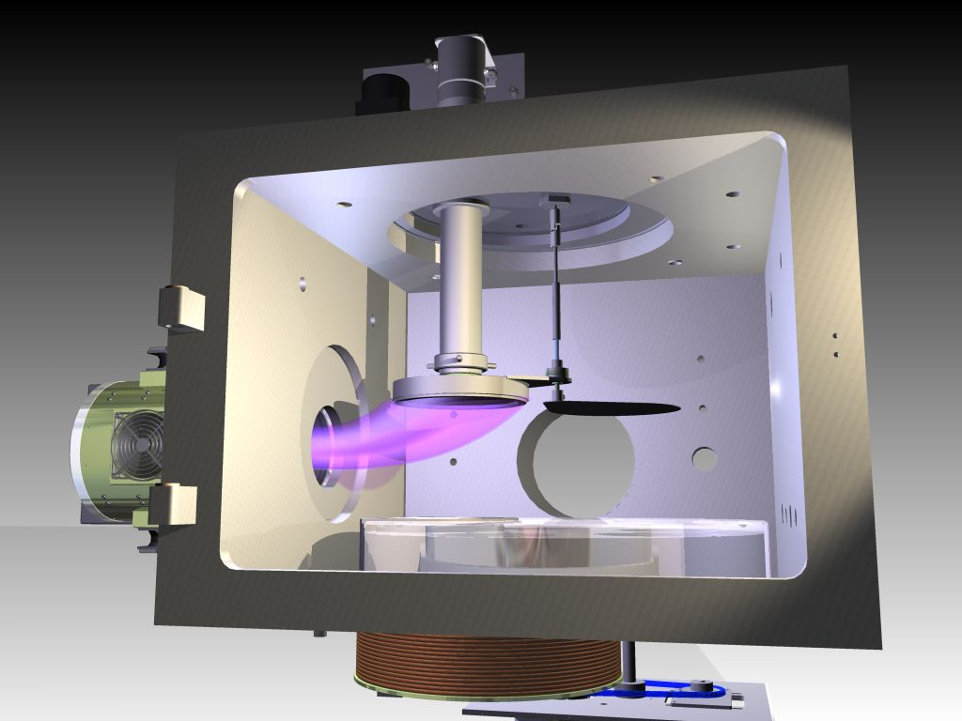
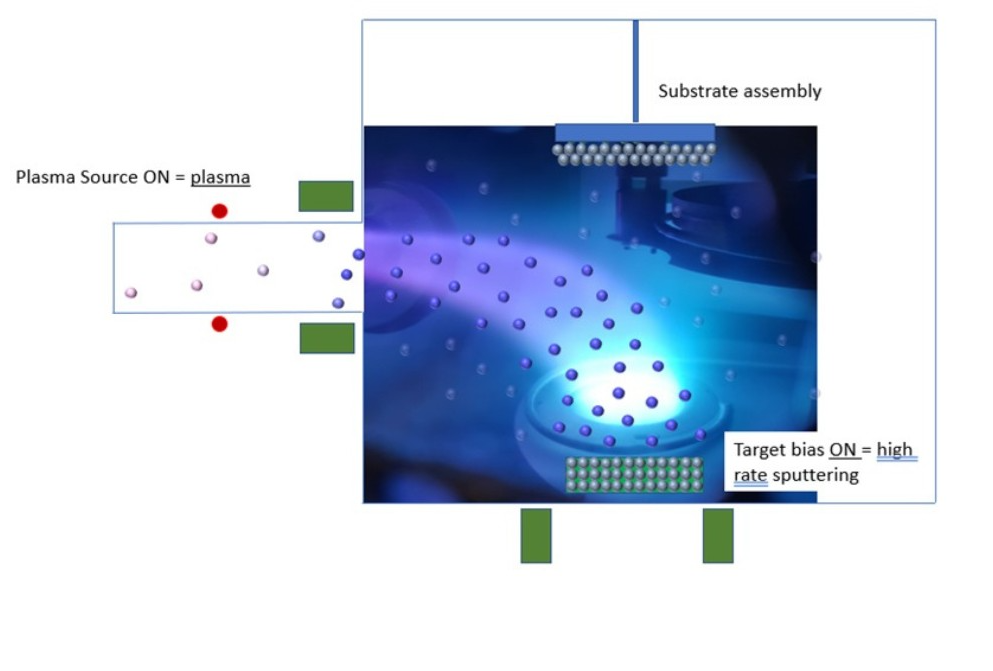
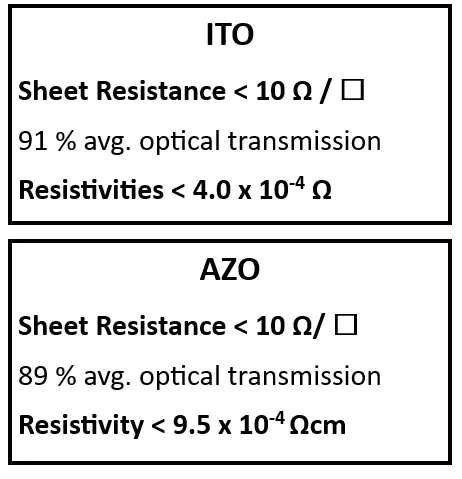
Low Temperature Process
Low temperature deposition onto polymeric and other 'delicate' substrates
The plasma provides energy input to the coating process instead of substrate heating
Deposition onto polymeric substrates; (PEN, PET, BOPP, PES, PMMA etc)
Deposition on to delicate materials (e.g. OLEDs, photoresist, etc)
Very little electron damage; electrons constrained by DC electromagnetic field
High Target Utilisation
Whole target surface continuously sputters
Stable and repeatable coatings, especially for oxides and nitrides as target is not poisoned
Reduces both costs and waste
No "race-track"
High deposition rates of > 80 nm/min from 4" diameter targets
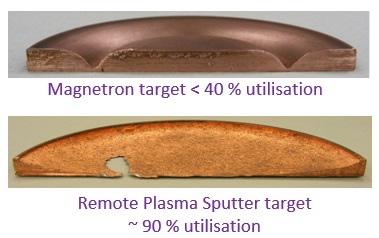
Stable, High-Rate Reactive Process
Remote Plasma offers enhanced deposition rate, process stability & simplicity when compared to conventional sputtering
Reactive processes completed without target poisoning due to uniform surface erosion
No need for feedback control when reactive sputtering
Addition of reactive gas increases deposition rate beyond that of the pure metal
Good control of stoichiometry; enabling deposition of complex materials such as Ti4O7 and Cu4O3
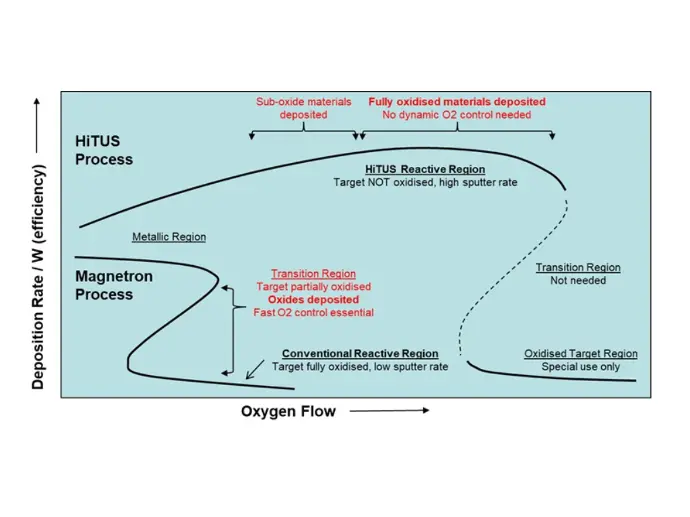
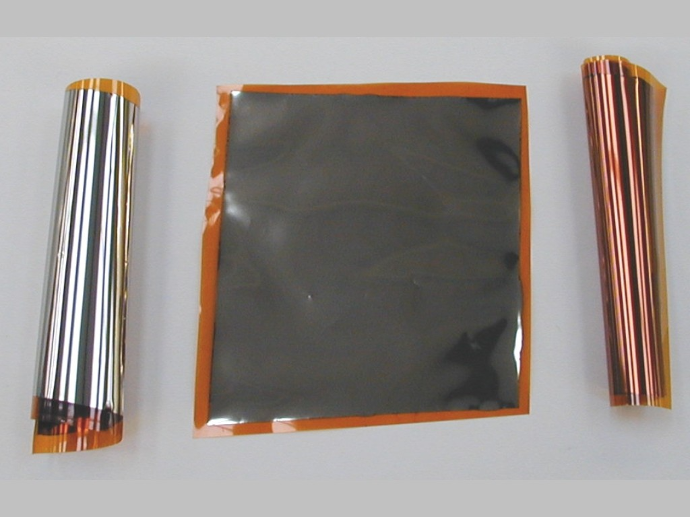
Stress Control
Due to our unique remote plasma process, the technology can be used to control the stress within thin films from compressive through to tensile
In magnetron sputtering the process pressure is varied to control stress
In Remote Plasma Sputtering the stress is controlled by process pressure and target voltage - extra process parameters to control stress
Thick Ferromagnetic Targets
No magnets directly behind the target.
Ability to sputter from thick ferromagnetic targets: less system downtime
Materials we have experience depositing:
- Fe, Co, Ni, CoFe, NiFe, Inconel, NdFeB
We have achieved stress free thick ferromagnetic coatings with good adhesion
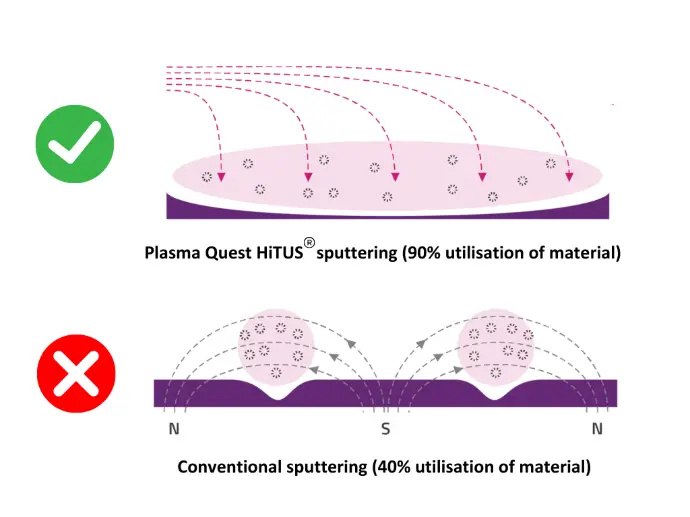
Ionised Physical Vapour Deposition
The high density plasma can ionise a significant fraction of the sputter flux
With an electrically biased substrate it can influence the directionality and energy of the arriving ionised material
Enables conformal coverage of high aspect ratio substrates and other complex topographies
Image shows an EDX map demonstrating that the RF substrate bias can be tuned to produce a uniform and conformal coating of thin film Al2O3
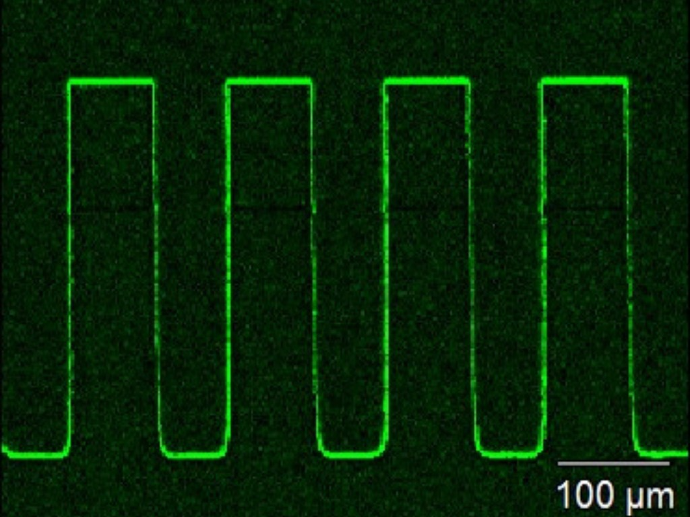
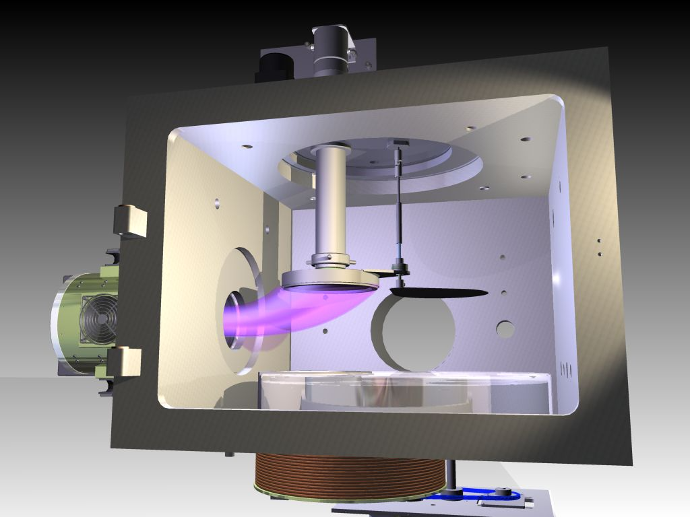
High Adhesion of Coating
Can immerse substrates in high density plasma prior to deposition to help promote good adhesion
Plasma assist improves adhesion, often eliminating the need for tie interlayers

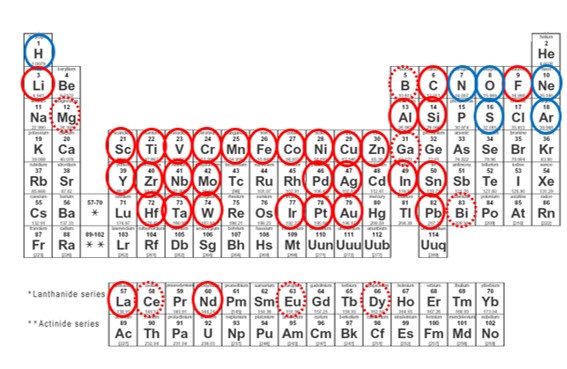
Wide Range of Materials
Metals, magnetic materials, TCOs, dielectrics, polymers
Periodic table opposite highlighting the materials we have experience with. Remote Plasma Sputtering could potentially be used to deposit those materials not highlighted but, to date, these have not been attempted
Control of Crystallinity
Films can be deposited with an amorphous or crystalline structure by controlling the plasma energy during growth
Image shows the effect of increasing plasma source power for an ITO coating
Substrate Plasma-Treatment
The Remote Plasma nature of the process means that inherently the system enables the substrate to be plasma treated;
This can be done with a number of gases
Offers enhanced adhesion performance
Plasma Quest developed a unique plasma treatment during a government funded program (InREP) that enabled an ohmic contact to be achieved between our AZO coatings and the doped GaN substrate
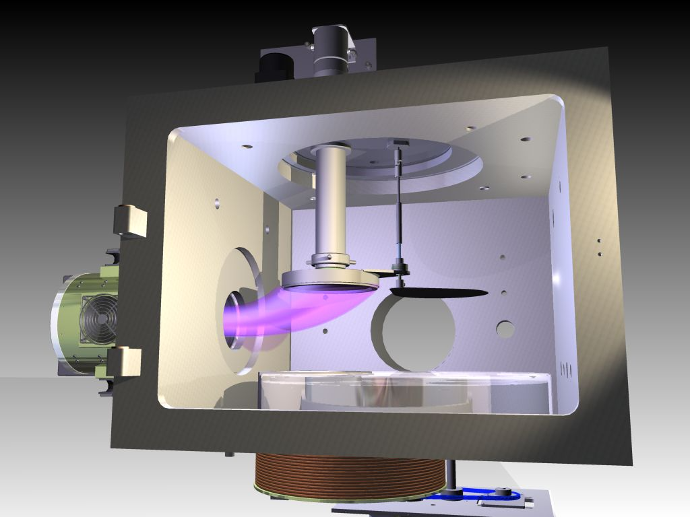
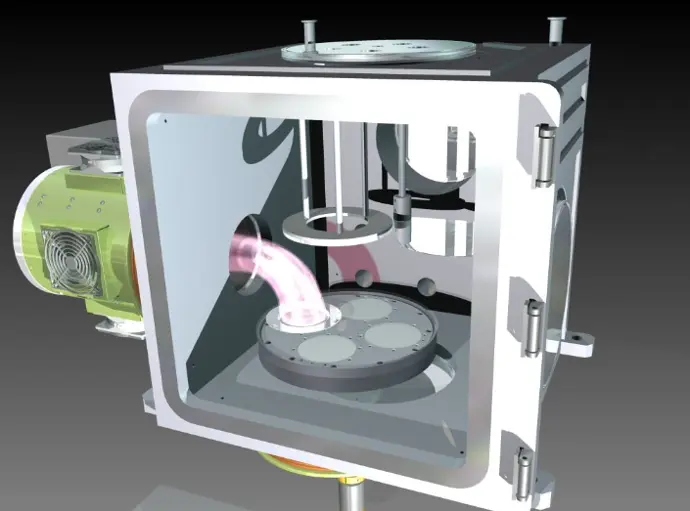
Substrate etching
With substrate bias, uniform etching of the wafer can be achieved